Operators need to scrutinise and interpret the results of roller brake-testing, and not just rely on seeing the word ‘pass’ on the bottom line of the generated report.
That was a key message from the first of this year’s FTA Transport Manager conferences, which was held at the Haynes Motor Museum in Somerset.
Western area traffic commissioner Kevin Rooney provided the keynote address for the conference, and explained that roller brake testing had been used in the industry for at least 50 years, but was not the be-all and end-all of assessing brake condition.
While the annual test focussed on performance, he pointed out that the Construction & Use Regulations (C&U) which every vehicle had to conform to every day it was on the road were actually stricter. C&U stipulated that every part of the braking system had to be in “good and efficient order”.
“This means it must be to the manufacturer’s standard,” he said. ”A detailed brake test needs to cover every part of the system.
“But unladen testing is meaningless.” He showed the results for a Volvo tractor unit that had been tested unladen. It had passed the test in terms of service brake performance, but the brake on the second axle had locked up having generated only 650 kg of braking force, as there was insufficient weight on the wheels.
“This is not representative,” he said. “During heavy braking, most of the trailer weight will transfer to the tractor, so testing things empty is a waste of time.”
Reputable testers either use loading-beams to transfer force onto the vehicle to simulate a load, or used water-filled intermediate bulk containers (IBCs) or similar to create one.
“Roller testing an unladen vehicle nullifies the inspection,” he warned.
Later in the conference, Phil Lloyd, head of engineering and vehicle standards at FTA (pictured, right), added more detail.
“Operators take false comfort from the word ‘pass’ at the foot of a brake test report,” he said. “It’s a piece of evidence that says everything is alright when really it isn’t.”
Operators were normally required to put every vehicle and trailer through four equally-spaced brake tests, one of which could be the annual test, every 12 months.
“Annual tests and periodic maintenance inspections both have the same objective: making sure the vehicle is in safe, roadworthy condition.”
He warned operators that every line of the printed paper report generated by the brake test should be scrutinised, starting at the top.
“Look for the DTp number at the top of the report. This identifies the vehicle, its specified brake performance, and plated weight. Check it against the number on the vehicle’s plating certificate. If this number is wrong, then the report is worthless.”
It was necessary to understand how the brake tester worked if the results it generated were to be understood. Vehicles were tested one axle at a time, and each wheel was positioned in a pit which contained two driving rollers coated in a high grip material to drive the wheel, and a single sensing roller between and beneath them which sensed the wheel’s rotation.
The wheel was rotated by the driving rollers, with the tyre driving the sensing roller beneath. During the brake test itself, the brake is strongly applied to create resistance between the tyre and the driving rollers, and the sensing roller measures the amount of resistance being offered by the brake in kg force.
Overall brake efficiency is calculated by adding the braking force generated by each wheel and dividing the total by the weight of the vehicle (GVW for rigids, GTW for tractors and TAW for trailers). The resultant figure is then multiplied by 100 to give a percentage efficiency.
However, this calculation can only be meaningful if there is a reasonable force acting on the tested axle to maintain traction between tyres and driving rollers. Each axle should be loaded to between 50 and 65 per cent of its design weight, and the brake tester will measure this.
However, if the axle is not sufficiently laden, then grip will be lost and the wheel locked before maximum efficiency is recorded. The system will record a wheel lock as a pass, but the report will give no indication of the brakes’ actual efficiency.
Mr Lloyd cautions: “If you want a meaningless brake test, put the truck on the rollers unladen and bang the brakes on; if the brakes lock up, then you’ve passed!”
He pointed out other deficiencies with the brake test.
Drum ovality (or rotor run-out in the case of discs) was only tested on the front axle. The test rig picked up variations in braking effort as the wheels rotated slowly with the brakes only marginally applied.
Wheels were each tested individually, but the effort generated on each side of a single axle could show an imbalance of up to 30 per cent and still pass.
“There is a potential issue with steering control under braking at this point,” he said. “It should at least be an advisory.”
He urged operators to take advantage of the data generated by the electronic brake performance monitoring systems fitted on most new trailers.
“It gives an indication of brake performance in real-time and can also indicate braking problems with the towing vehicle,” he said.
More details are contained in the Brake Test Report, published by the FTA last month, and given to each delegate at the conference.
Brian Beacon, director of roller brake testing equipment specialist VL Test Systems (VLT), commented: “VLT always carry out full in-depth training when installing our brake testers, covering the full printout and explanations for each section.
“Our recommendation is that the vehicle/trailer is loaded to 65 per cent minimum for a meaningful test, and if it is not then a warning is shown on the screen and the printout stating ‘insufficient load on axle’.
“We are aware of items that could be improved but to gain DVSA approval for the equipment in automatic mode, we have to follow DVSA rules setting out the full test as it is at present, including the ‘locks rule’.”
He added: “All our brake testers also have different modes whereby the tester can carry out full checks on each wheel or axle including individual brake force, bind, ovality, imbalance etc – and even draw graphs to visually compare these figures.
aide automotive offer the simple tool of a Infra Red Gun for Truck & Trailer Brake Checks.
DVSA Guidance states The Use Of a Temperature Tool Is Good Practice For Commercial Vehicle Maintenance Routines. Extract From Guide to maintaining roadworthiness (11.2018) “The use of brake temperature measurement can improve the effectiveness of a road test and is an established method to assess if individual brakes are operational. Brake disc/drum temperature readings should be compared across an axle after a laden road test or by in-service monitoring, using a brake temperature sensor, which can be a simple handheld device or using a more sophisticated remote monitoring system. Brake temperature readings would need to be well above ambient temperature with relatively consistent readings taken for each brake across an axle. Brakes which are cold (ambient temperature) or showing an inconsistent reading from the brake on the opposite side on the same axle, should be investigated further.” Simple & Hand Held !
Buy A Temperature Gun From aide automotive For Just £15.95 + post & VAT! Buy Online https://bit.ly/33kRGAw
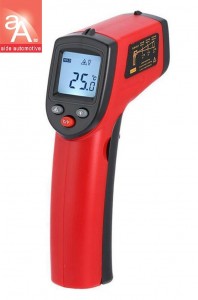
HGV Brake Checks With A Temp Gun